Introduction:
Welcome to our comprehensive guide on air oil coolers! Whether you’re an automotive enthusiast, an industrial machinery operator, or simply curious about cooling systems, this blog post will provide you with all the essential information about air oil coolers. These devices play a crucial role in maintaining optimal temperatures for lubricating oil, ensuring the smooth operation and longevity of various mechanical systems. So, let’s dive in and explore the world of air oil coolers together!
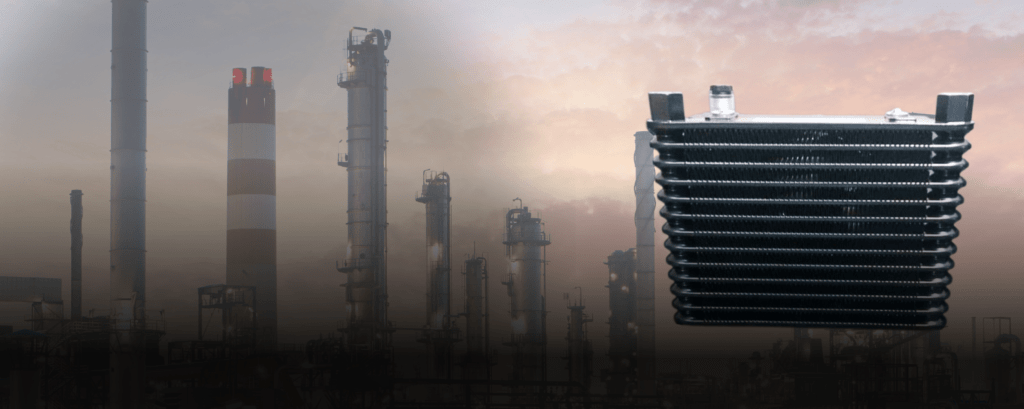
What are air oil coolers ?
Air oil coolers are heat exchangers designed to remove excess heat from lubricating oil used in engines, transmissions, hydraulic systems, and other applications. They utilize the ambient air to cool the oil, thereby preventing it from overheating and ensuring consistent performance. By dissipating heat efficiently, air oil coolers help protect the machinery from damage caused by excessive temperatures.
- Working principles: Air oil coolers work on a simple yet effective principle. The hot oil flows through a network of small tubes or passages within the cooler, while air is forced or drawn across these tubes to remove heat. The heat transfer occurs through conduction and convection, as the hot oil transfers its thermal energy to the metal walls of the cooler, and the airflow carries away the heat. This continuous process helps maintain the oil temperature within the desired range.
- Air-to-Oil Heat Exchangers: In this type, oil flows through a series of plates or coils while air passes over them. The heat transfer occurs between the oil and the plates/coils, ensuring efficient cooling. Air-to-oil heat exchangers are often used in larger industrial applications where high cooling capacity is required.
- Air-Cooled Finned Tube Coolers: These are the most common type of air oil coolers, consisting of a core with numerous small tubes surrounded by fins. The fins increase the surface area, enhancing heat dissipation. Air is either blown directly over the fins using fans or naturally circulated through the cooler by the movement of the machinery.
Benefits of Air Oil Coolers:
- Enhanced Lubricant Performance: By maintaining optimal oil temperatures, air oil coolers prevent oil breakdown and maintain its lubricating properties, leading to better overall performance and reduced wear and tear.
- Extended Machinery Lifespan: Cooling the oil effectively helps extend the life of mechanical components, reducing the risk of costly repairs or premature equipment failure.
- Improved Efficiency: Proper temperature control provided by air oil coolers ensures that machinery operates at its peak efficiency, reducing energy consumption and increasing productivity.
Applications of air oil coolers:
- Automotive: Engine oil coolers, transmission oil coolers, power steering coolers.
- Industrial: Hydraulic system coolers, compressor coolers, generator coolers.
- Marine: Marine engine oil coolers, transmission oil coolers.
- Agriculture: Tractor hydraulic oil coolers.
Conclusion
Air oil coolers are indispensable components in maintaining efficient and reliable operation of engines, machinery, and hydraulic systems. By preventing oil overheating, these coolers contribute to enhanced performance, extended lifespan, and improved energy efficiency. Understanding their working principle, types, and benefits will empower you to make informed decisions when it comes to selecting and maintaining air oil coolers. Remember to consult professionals and follow manufacturer recommendations to ensure the best outcomes for your specific applications. Stay cool, stay efficient!
Note: we also customized our products as per customer demand.